Nylon materials prepared through ring-opening polymerization or condensation polymerization using raw materials obtained via bioengineering methods are collectively referred to as bio-based nylon materials. Common bio-based nylon materials include nylon 11, nylon 1010, nylon 610, nylon 510, nylon 410, and nylon 1012, among others.
Below is an overview of the reinforcement modification of bio-based nylon:
1. Reinforcement Modification of Nylon 1010
Similar to the fillers used for reinforcing nylon 11, researchers primarily employ various fibers and clays for reinforcing nylon 1010.
(1) Carbon Fiber Reinforcement
- In a twin-screw extruder, two types of nylon 1010 with different tensile strengths were melt-blended with carbon fibers.
- For higher tensile strength pure nylon 1010, adding 20% and 40% carbon fibers increased the tensile strength from 51.4 MPa to 158.0 MPa and 184.9 MPa, respectively. The elongation at break decreased from 89% to 4.5% and 3.8%.
- For lower tensile strength pure nylon 1010, adding 10% and 30% carbon fibers increased the tensile strength from 26.7 MPa to 71.1 MPa and 102.8 MPa, respectively. The elongation at break decreased from 277% to 10% and 6.2%.
- As the carbon fiber content increased, the crystallization temperature of the blend gradually increased, while the crystallinity decreased.
(2) Rice Husk Ash and Nanoclay Reinforcement
- In a twin-screw extruder, nylon 1010 was melt-blended with rice husk ash and nano-montmorillonite.
- When 10% and 20% rice husk ash were added, the tensile strength of the blend decreased from 46.2 MPa (pure nylon 1010) to 41.2 MPa and 36.4 MPa, respectively. This was attributed to interfacial defects and inefficient stress transfer from the polymer matrix to the filler.
- The Pukanszky model was used to describe the tensile behavior of the blend, confirming the above inference. When 5% nano-montmorillonite was added, the tensile strength increased to 44.0 MPa.
- As the rice husk ash concentration increased, the heat deflection temperature (HDT) of the blend at 0.46 MPa rose from 109°C (pure nylon 1010) to 144°C and 174°C. After adding 5% nano-montmorillonite, the HDT exceeded 180°C.
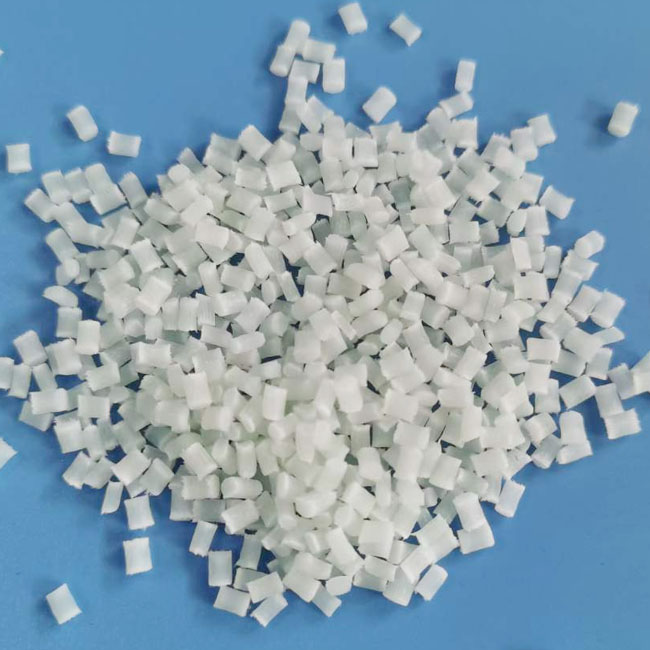
(3) Graphene Reinforcement
In a twin-screw extruder, nylon 1010 was melt-blended with graphene to study its effect on polymer chain mobility and crystallization. It was found that the amide groups in the amorphous region of nylon 1010 chemically reacted with graphene, promoting interlayer exfoliation and dispersion of graphene in the nylon matrix.
- When 5% graphene was added, the tensile modulus of the blend reached 1780 MPa, 1.8 times that of pure nylon 1010, while the yield strength was 44.7 MPa, 1.4 times that of pure nylon. The elongation at break decreased from 58% (pure nylon) to 23%.
- The melting enthalpy of the blend and pure nylon was 67.3 J/g and 59 J/g, respectively, and the thermal stability of the polymer increased by 10°C.
(4) Slate Fiber Reinforcement
In a twin-screw extruder, nylon 1010 was melt-blended with slate fibers treated with oxypropyl and amino silane coupling agents, significantly improving the compatibility between nylon 1010 and the fibers.
- Slate fibers treated with oxypropyl coupling agents showed the best reinforcement effect. When the mass ratio of nylon 1010 to slate fibers was 85:15, the tensile strength of the blend increased from (56.7 ± 1.3) MPa (pure nylon 1010) to (111.2 ± 1.4) MPa, while the impact strength remained almost unchanged, demonstrating excellent reinforcement.
2. Reinforcement Modification of Nylon 11
In studies on the reinforcement modification of bio-based nylon, lignocellulose, lignin, and mixed fibers are commonly used as fillers for modifying nylon 11. These natural fibers exhibit excellent reinforcement effects due to their abundant hydroxyl and oxygen-containing functional groups, which can chemically react or form hydrogen bonds with the amide groups or terminal amine and carboxyl groups of bio-based nylon during melt blending. This significantly improves the dispersion of natural fibers in the nylon matrix and enhances the mechanical properties of the material under external impact.
(1) Lignocellulose Reinforcement
studies were conducted on the preparation, performance characterization, and calculation of nylon 11/lignocellulose blends.
- As the mass fraction of lignocellulose increased from 20% to 60%, the notched and unnotched impact strength of the blend gradually decreased.
- The water absorption behavior was studied using contact angle and Fickian diffusion theory. As the lignocellulose content increased, the water contact angle decreased, and water absorption increased. At 23°C and 40°C, the Fickian diffusion coefficient of the blend with 60% lignocellulose was more than double that of the blend with 20% lignocellulose.
(2) Lignin Reinforcement
Untreated lignin was used as a filler to reinforce nylon 11 in a twin-screw extruder, producing fully bio-based nylon composites.
- The addition of lignin hindered the crystallization of nylon 11 and increased the yield stress and Young’s modulus of the blend. However, the elongation at break depended on the lignin content: it remained similar to pure nylon 11 when the lignin content was below 12.5% but decreased significantly when the lignin content exceeded 12.5%.
(3) Nanocellulose Reinforcement
Nylon 11 was melt-blended with nanocellulose in a twin-screw extruder.
- Nanocellulose did not affect the crystallization behavior of the nylon 11 matrix. When 0.5% nanocellulose was added, the tensile strength and impact strength of the blend increased by 23% and 67%, respectively, compared to pure nylon 11.
- When carboxymethyl cellulose was used as a compatibilizer for blending nylon 11 with glycerol-modified starch, the blend with 70% starch exhibited a tensile strength of 20 MPa and an elongation at break of 150%, showing excellent mechanical properties. Rheological and SEM analysis revealed a bicontinuous distribution of starch and nylon.
(4) Mixed Fiber Reinforcement
Instead of using a single fiber, nylon 11 was melt-blended with a mixture of wood fiber and carbon fiber in a twin-screw extruder.
- The tensile strength of the blend was 46% higher than that of nylon 11/wood fiber blends. When polypropylene was added, the tensile strength further increased by 13%, and the impact strength increased by 58%, while the cost was reduced.
- SEM images showed that the fibers were well dispersed in the polymer matrix with good adhesion. The heat deflection temperature of the blend with polypropylene was 30°C higher than that of nylon 11/wood fiber/carbon fiber blends.
- The nylon 11/polypropylene/wood fiber/carbon fiber blend, with its low density, low cost, and superior mechanical properties, is highly suitable for automotive applications.
3. Reinforcement Modification of Other Bio-Based Nylons
While research on reinforcement modification has been extensive for nylon 11 and nylon 1010, studies on other bio-based nylons, such as nylon 610, nylon 510, and nylon 410, are relatively limited.
(1) Nylon 510 Reinforcement
Glutaric acid was prepared through metabolic engineering and polymerized with sebacic acid to produce bio-based nylon 510.
- The intrinsic viscosity reached 141 mL/g, with a melting point of 215°C, close to that of nylon 6 and nylon 66. The density was 1.07 g/cm³, lower than that of nylon 6 and nylon 66 (1.14 g/cm³).
- When melt-blended with 30% glass fiber in a twin-screw extruder, the tensile strength of the blend was 155 MPa, slightly lower than that of nylon 6 and nylon 66 (179 MPa and 188 MPa, respectively). The elongation at break was 3.9%, slightly better than that of nylon 6 and nylon 66 (3.8% and 3.7%, respectively), and the notched impact strength was 12 kJ/m², superior to that of nylon 66 (10 kJ/m²).
(2) Nylon 410 Reinforcement
Nylon 410 was melt-blended with acetic acid-treated microcrystalline cellulose in a twin-screw extruder.
- After treatment, the thermal stability of cellulose improved, facilitating its dispersion in the nylon matrix. When the cellulose content was between 1% and 5%, the melting point and crystallization temperature of the blend gradually decreased, while the storage modulus increased.
Toughening Modification of Bio-Based Nylon
Toughening modifiers for bio-based nylon are often non-polar polyolefins, while nylon is a polar polymer. To achieve effective blending, grafted compatibilizers, typically using maleic anhydride as the grafting monomer, are added. During melt blending, the maleic anhydride in the compatibilizer reacts in situ with the terminal amine and carboxyl groups of the nylon chains, forming grafted compounds with interfacial compatibility. This significantly improves the dispersion of the toughener and enhances the material's toughness by effectively transferring impact stress from the matrix to the toughener phase.
url: https://yanmeiplastics.com/news/reinforcement-modification-and-Applications-of-Bio-Based-Nylon.html